Special
Warehouse & Logistics at Ginzinger
We talk to DI Cecilia Bergström, Head of Warehouse/Logistics about the current challenges in the company.
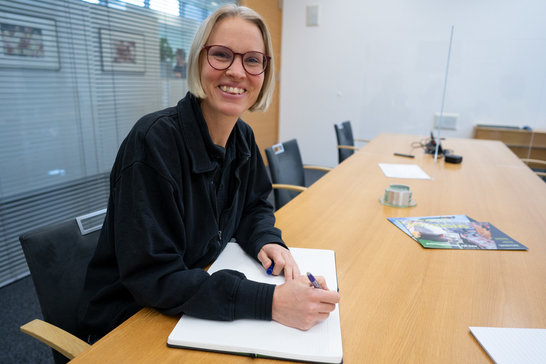
Cecilia, warehouse and logistics are an important linchpin for the smooth production of our customer products. In short, nothing works in production without you guys.
Cecilia: That's right (laughs): We are needed everywhere and are the point of contact for many departments. We have inventory sovereignty over the material, i.e. also over bookings and stocks.
Our incoming goods department takes care of all the materials that are delivered to us. It unpacks them, checks them and posts them to the ERP system. From there, the picking team takes over the storage on the shelves. During picking, we prepare all material for assembly production. After production is completed, we receive the produced assemblies (customer and semi-finished products) back.
At goods issue, a lot of know-how about our different customers and their products is necessary. Each customer item has its own customized packaging including shipping instructions. We ship assembled electronic assemblies as well as completely assembled customer devices including operating instructions and specific customer packaging.
You have already gained a lot of experience in the field of logistics. What has your professional career been like?
Cecilia: I was born in Sweden. There I studied industrial engineering with a focus on logistics. I have been in Austria since 2002 and was logistics manager in a food manufacturing company for ten years. My focus there was on lean management. After that, I worked for a medical equipment manufacturer as a lean team leader - until I landed at Ginzinger. I am very happy about that.
What goals have you set for yourself as logistics manager at Ginzinger?
Cecilia: The main task was to optimize the processes. Another major task that had to be implemented was to make the best possible use of the available storage space. Due to the great order situation, as well as stock purchases to ensure the availability of material, we are bursting at the seams at the Weng site. Today, we have twice as much material in stock as we did a year ago. The aim was therefore to make the best of the current space situation. The currently ongoing addition of a production hall, which is scheduled for completion by July 2022, is an important step towards creating more space.

The topic of "warehouse optimization" has kept you very busy over the past year.
Cecilia: Yes, very much so. We have completely reorganized and restructured the warehouse. All the shelves in the warehouse were rebuilt. The warehouse lifts were reorganized. Additional, external storage space and containers for bulky material were also rented. The bottom line is that we got the most out of it. This is also reflected in the figures. Picking times of components were reduced by defined and smaller storage bins. The storage locations, as well as the storage or inventory value, have doubled while the storage area has remained the same.
What challenges are you facing in the near future?
Cecilia: Of course, on the one hand, we are concerned with the issue of developing our employees. Flexible employees who can support colleagues when needed are important to me. That's why we want to train several people at different workplaces. Secondly, we want to further optimize the warehouse and logistics.
Setting up the new warehouse and phased settling will have a strong impact on 2022. We are getting three new warehouse lifts. Here, all the material will first be removed from storage and later put back into storage. All this will happen during ongoing operations. That will certainly be a challenge.

New technical highlights are also planned, such as a wrapping and a lacing device for outgoing goods. We converted some products to kanban in 2021. We want to continue this in 2022 for other products where it makes sense. I'm thinking of common consumables, among other things.
When receiving goods, we try to avoid unnecessary packaging and cumbersome repackaging or repackaging. Here we work together with the purchasing department. In this way, we can contribute a little to environmental protection by saving on packaging waste.
Cecilia, thank you for the interview!