Challenge
Innovative Mini-5-Achs-Fräse
Für die rasche Serientauglichkeit einer Fräsenelektronik beauftragte die DMU GmbH aus Salzburg Ginzinger electronic systems mit der Optimierung und Integration der elektronischen Komponenten.
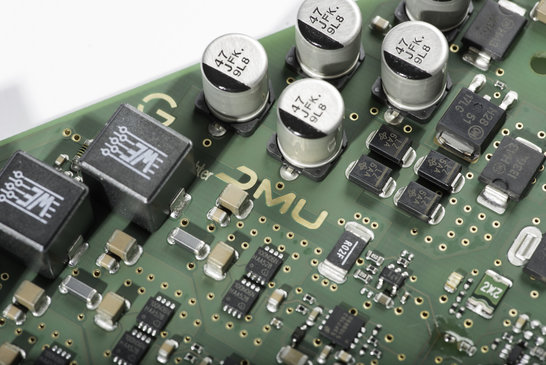
Wozu in die Ferne schweifen, wenn das beste liegt so nah? Hard- und Softwareentwicklung aus einer Hand für die kleinste 5-Achs-Fräsmaschine der Dentalwelt.
DMU GmbH
Die DMU (Dental Manufacturing Unit) GmbH mit Sitz in Salzburg realisiert anspruchsvolle CNC-Technologie und bietet präventive Instandhaltung und Softwareentwicklung. Technologisch führend in diesem Bereich, entwickelt das Unternehmen Spezialmaschinen für die Bearbeitung von Zahnrohstoffen.
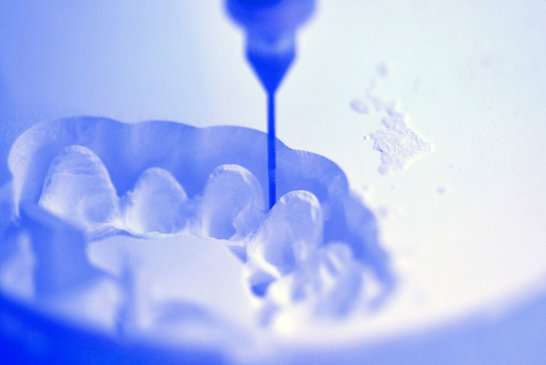
Kleinste Fräse der Dentalwelt
Es begann mit der Erfindung der kleinsten 5-Achs-Fräsmaschine der Welt für die Dentalmedizin. Das Salzburger Start-up-Unternehmen DMU GmbH, das mittlerweile ca. 30 Mitarbeiter Innen zählt, entwickelte diese bis zur Serienreife. Um die Anpassungen vom Prototypen bis zum fertigen industrietauglichen Produkt vorzunehmen, waren Änderungen an der bisher verwendeten Proof-of- Concept-Elektronik nötig. Der Druck zur Finalisierung des Produkts war enorm, da eine Vorstellung auf der größten Dentalmesse der Welt im Frühjahr 2017 geplant war. Um die Fräsenelektronik rasch serientauglich umzusetzen, beauftragte DMU Ginzinger electronic systems mit der Optimierung und Integration der elektronischen Komponenten.
Dentalfräse
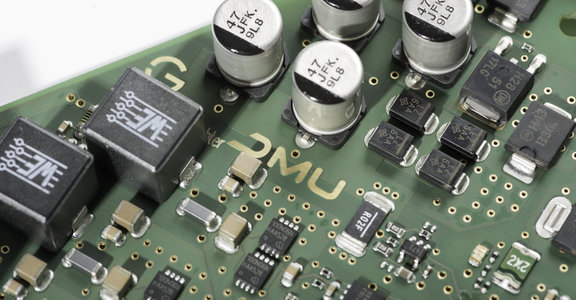
Projektstart
Integration & Designoptimierung
Der Projektstart erfolgte umgehend. Die Hardware der Prototypen war ursprünglich auf viele Platinen mit hohem Verdrahtungsaufwand ausgelegt. In der Serienproduktion wäre dieser Aufwand nicht tragbar. Das Ziel war daher, alle Funktionen auf zwei Platinen – einem IO-Board und einem Spindelcontroller-Board – neu zu integrieren und so zu designen, dass diese ideal an das Fräsmaschinengehäuse angepasst und thermisch gesichert sind. Darüber hinaus sollten der Montage aufwand minimiert sowie Hardware- und Softwarefunktionsgruppen logisch und wirtschaftlich optimiert werden.
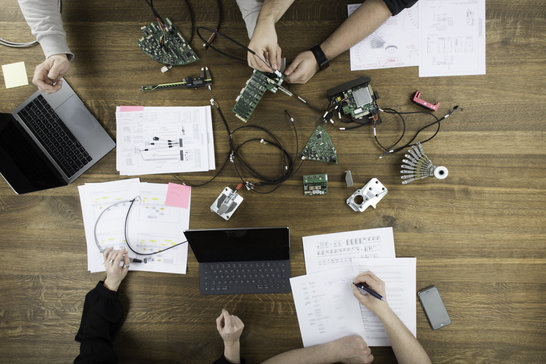
Innovation auf kleinstem Raum
Die beengte Raumsituation der kompakten Minifräse stellte das Design vor einige Herausforderungen. Dazu zählen beispielsweise ein zu optimierendes thermisches Management sowie die EMV. Die Konzeption der IO-Platine war dabei zeitintensiver als gedacht. Durch die Streuung der Parameter bei einer Flüssigkeitspumpe gab es zudem sporadische Ausfälle. DMU konnte hier mechanisch eingreifen und optimieren.
Zusätzlich versuchte das Team von Ginzinger, mittels der Softwaretreiber am IO-Board eine verbesserte Ansteuerung der Pumpe zu erreichen, und analysierte durch Experimente und Messungen die Pumpenparameter.
"Bei Ginzinger arbeiten Softwareentwickler und Hardwaredesigner sehr eng zusammen. Problemstellungen werden in ihrer Gesamtheit untersucht. Auch bei dieser Aufgabenstellung fand man im Team die perfekte Lösung und unterstützte DMU bei der weiteren Optimierung seiner Lieferkette."
Partnerschaftliche Umsetzung
DMU & Ginzinger
Ginzinger arbeitet in vielen Projekten mit einer eigenen Embedded Run-Time auf Microcontroller-Basis. Diese vereinfacht die Entwicklung, die Tests und die Serienproduktion und arbeitet seit vielen Jahren in zigtausenden ausgelieferten Geräten. Auch DMU setzt diese Run-Time als Plattform für die Softwareentwicklung auf dem IO-Board ein. Während das Anwendungs-Know-how somit gänzlich bei DMU bleibt, setzen die Implementierung der Software und das komplexe Ablaufmanagement auf die beständige Firmware von Ginzinger.
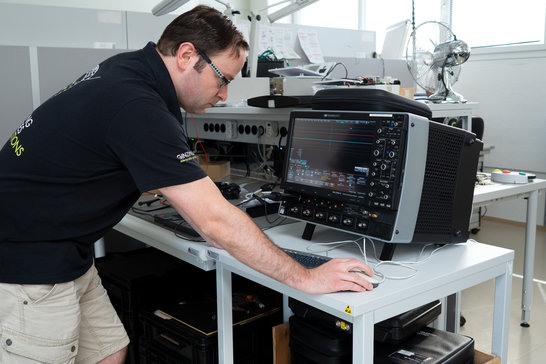
Kostenreduktion durch erprobte Prozesse
Microcontroller sind aus modernen elektronischen Komponenten nicht mehr wegzudenken. Doch statt diese immer wieder mühsam bare-bone zu programmieren und das Rad neu zu erfinden, bewährt sich eine schlanke Run-Time-Firmware über den gesamten Lebenszyklus der Elektronik.
Man setzt auf ein robustes, tausendfach bewährtes Fundament, vereinfacht die Entwicklung mittels schlüsselfertiger Bibliotheken, kann sich bei der Wartung der Plattform auf einen erfahrenen Partner verlassen und bekommt darüber hinaus Testroutinen auf IO-Ebene frei Haus mitgeliefert. Alles in allem führt das zu einer großen Erleichterung für alle Projektbeteiligten und zu einer wesentlichen Reduktion der Gesamtkosten.
Enge Zusammenarbeit
Ergebnis: Eine optimale Lösung
Durch das gemeinsame Projekt entstand eine enge Zusammenarbeit zwischen DMU und Ginzinger electronic systems. Optimierungen und Erweiterungen am Produkt werden weiterhin laufend gemeinsam durchgeführt. „Wir freuen uns, dass wir mit Ginzinger electronic systems einen verlässlichen Partner, noch dazu ganz in der Nähe, gefunden haben, der uns rasch und unbürokratisch bei der Realisierung unserer Ideen unterstützt hat“, sagt Martin Huber, Technischer Geschäftsführer der DMU GmbH.

„Die Erfahrung, aber auch viele neue Ideen der Ginzinger-Techniker haben wir gerne in unsere Produktentwicklung aufgenommen. Auf dieser Basis konnten wir uns auch freispielen, um uns auf den Kundennutzen zu konzentrieren.“
Hard- und Softwareentwicklung als ideale Kombination
Das Projekt des Kunden DMU GmbH aus Salzburg zeigt, dass die Kombination von Hard- und Softwarentwicklung aus einer Hand, gepaart mit jahrzehntelangem Knowhow in der Produktion von Elektronikbaugruppen, zu optimalen Ergebnissen führt. Kunden profitieren von stabilen, industrietauglichen Produkten, die rasch realisiert werden können.